The top 20 tire producers manufacture a combined 1.5 billion units a year. This means a lot of space, time and manpower is dedicated to the storage, movement and delivery of each tire. Due to the evolution of digital technology, this is an area of the industry ready for a complete overhaul, and where tire manufacturers have the opportunity to make significant savings.
Historically tire movement and storage has almost always been carried out utilizing pallets, but in the modern world of digital technology and intelligent warehousing systems, palletizing is seen as inefficient, costly in terms of capital investment and a safety hazard. Add to that the fact that it’s also not good for the environment.
Finnish company Pesmel has developed a special smart warehousing system for the tire industry that is revolutionizing movement and storage of individual units. It is also being proven to save millions on investment in palletizing equipment and labor costs in tire plant warehousing.
Pesmel CEO Tony Leikas says, “The tire industry has generally seen palletization as the only solution for its warehousing and internal logistics needs. After looking closely at various plants around the world, and with our successful projects in other industries, it is clear to us at Pesmel that this is an area of the industry that could be much more efficient and run in a much safer and cost effective way.”
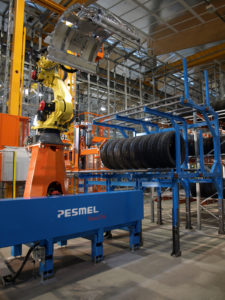
Simplified operations
Pesmel has developed a unique concept coined Material Flow How, which uses only four components to fully automate internal logistics and storage. The idea behind the concept is to arrange production and material flows so that production efficiency is maximized and the need for equipment minimized. In fact the Material Flow How concept only uses four components: a conveyor system, racking, stacker crane(s) and robots.
For the tire industry, the Material Flow How concept has been implemented into Pesmel’s bespoke designed TransTire AS/RS. The simplified, complete warehousing concept for tire storage includes the following four components:
Conveyors – the connecting link used to integrate the system from the production lines and transfer the tires from the manufacturing plant, into storage, and then further on when required for transportation.
Racking – tires are stored without using pallets, bringing efficiency to handling by saving time and space and using less equipment. This method of racking also eliminates the chance of damage that often occurs when using pallets.
Stacker crane – the TransTire stacker crane is an intelligent crane that combines storing and order picking.
Robots – TransTire works with robots as a two-machine team by preparing the tires for storage and further for shipping.
Pesmel’s Warehouse Management System (WMS) integrates and controls tire production flows between manufacturing, storing and shipping. The WMS can be fully integrated into the tire plant’s existing network and upper level control systems. The main task for the WMS is to control tire flow and optimize storage and logistical functions, which increases the total capacity of the system and brings down operating costs.
The storage systems are controlled automatically and unmanned by Pesmel’s own computer system, which comes with the necessary number of operator terminals. The WMS also features a wide range of reporting and diagnostical functions, to assist in maximizing efficiency even further.
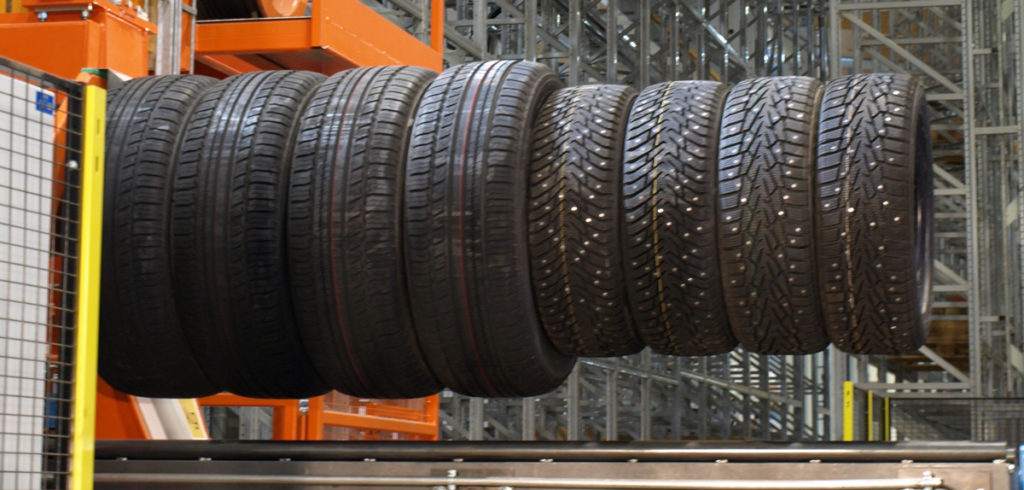
Delivering a fully functional system
According to Leikas, millions of euros could be saved when building a new tire plant by eliminating palletization completely: “Palletization equipment is expensive; our research tells us that up to €5m (US$5.5m) can be spent on installing the machines, which can be simply done away with by using a smart warehousing system. Eliminating palletization also creates up to 30% more space.
“Using pallets is also costly when it comes to warehousing operational efficiencies, with extra loading and unloading, bringing pallets in and sending them back again. Palletization is also labor intensive, often involving manual loading and unloading, and of course, there are the dangers presented with forklifts going backward and forward in a plant.”
The implementation of TransTire AS/RS starts with Pesmel experts building a simulation model of a customer’s tire plant warehouse, analyzing the production procedures and potential bottlenecks. The whole concept is then completely engineered in-house with Pesmel, taking care of all mechanical, electrical, PLC and ICT engineering. A fully functioning system is then delivered.