TTI speaks to Burkhard Wies, Continental’s vice president of research and development innovation and applied research, about some of the tire maker’s key areas of investigation
The continuing push toward cleaner and greener vehicles means more focus on tires and their overall contribution to the environment throughout their lifecycle. It’s a key topic for all tire manufacturers, including Continental. The obvious starting point is tires for electric vehicles. But, explains Burkhard Wies, Continental Tire’s vice president of research and development innovation and applied research, it’s not as big a deal as many may think. The increased torque and weight of EVs means more focus on lower rolling resistance and reduced wear, but these are things the tire industry is constantly looking to achieve across the board.
“Wear, noise and rolling resistance are all criteria that we have for every tire,” he says. “It’s a bit more pronounced and you normally have new sizes, tall and narrow because bigger wheels are better in terms of rolling resistance and wear. All our tires are EV-compatible so, if you have an EcoContact or a PremiumContact, it’s prepared to run as a tire on an electric vehicle, but also on a combustion-engined vehicle.”
Even so, research into new compounds better suited to EV tires has pushed for better wear without the corresponding compromises in wet grip and rolling resistance. However, there is also a need to reduce tire particulate emissions. Again, this is something that has come from low-emission vehicles such as EVs but applies across all tire use cases, and tallies with the drive for local and national legislation, which differs around the world.
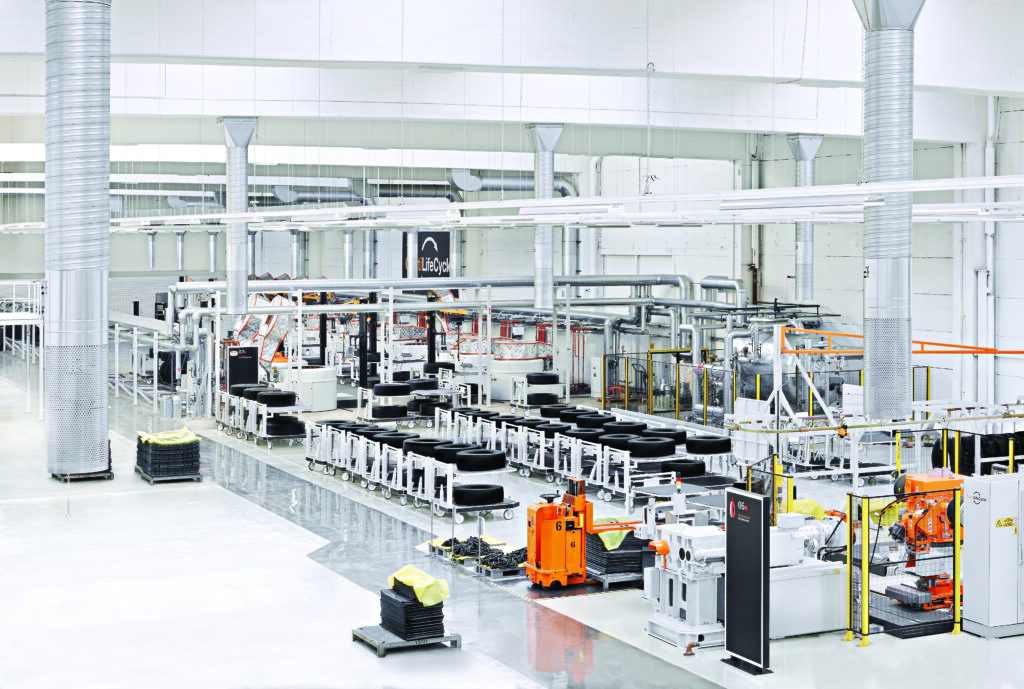
Wies and his team are not only conducting intensive research into ways of reducing particulate emissions, but are also investigating, for example, the formation of tire and road particles down to the molecular level in various internal and external projects in order to gain a holistic view. Continental is co-chair and founding member of the Tire Industry Project (TIP), an initiative that drives research on the potential impact of tires on the environment throughout their lifecycle.
With regard to the new Euro 7 standard, which requires binding limits for tire wear, Wies says that, for Continental it is important that the assessment is performed on the basis of internationally recognized test methods. It is crucial that the wear behavior of tires and the formation of tire and road wear particles can be measured and compared without the influence of external variables.
Design trends
Wies believes tire design is also a key element in terms of tread patterns, tire geometry and the physical composition of the tire, especially with regard to renewable and recycled materials. Other factors could also create significant changes, some of which are already being seen across the industry.
“Sizes will change, driven by the trend toward electric cars and speed limits,” he says. “Tire sizes will become bigger over time, also driven by autonomous cars, which could bring a change in the general geometry, but this is not clear just yet.”
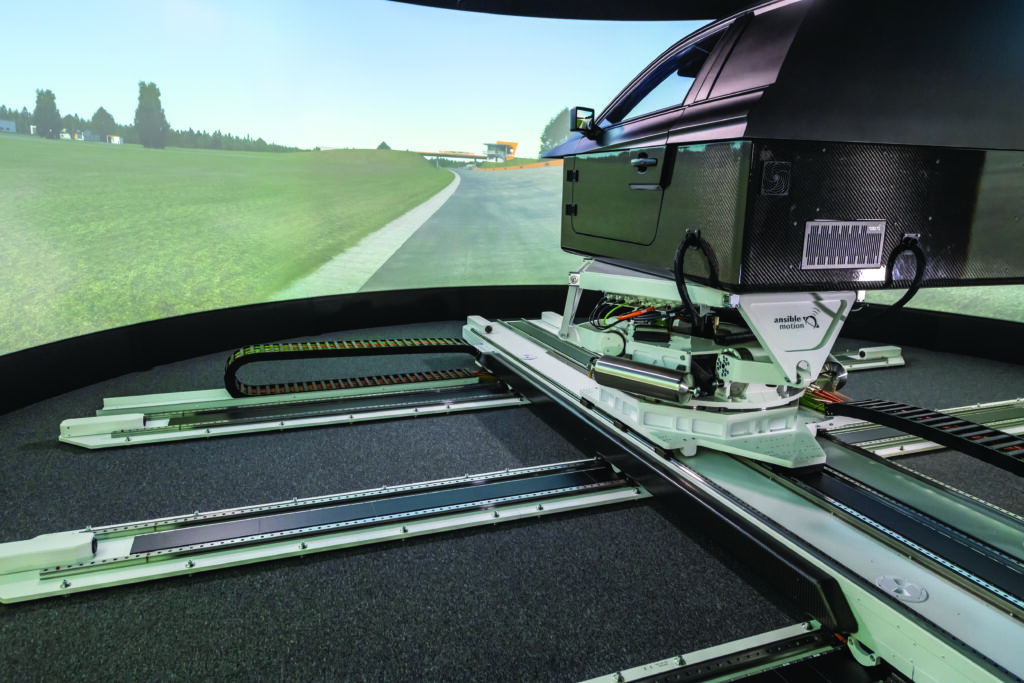
Continental recently launched its UltraContact NXT, which uses 65% renewable, recycled and mass balance-certified materials – a trend that Wies believes will become standard across the industry. However, due to material availability, such tires are currently more expensive than standard designs, and Wies stresses that although people talk about going green, he believes they aren’t always willing to pay for it.
Depth of field
Another area of particular design interest is tread depth, although Wies points out that there are obvious limits to how far this can go.
“We have 6mm, and to go beyond doesn’t make sense because of aquaplaning,” he explains. “There is a physical limit and if you go below 5.5mm it does not work anymore. Summer tires will be around 6mm, winter tires may go from 8mm to 7mm. The tire designs will become even more closed, with more rips [cuts], but also there is a technical convergence in terms of noise.”
That noise factor is very much a focus, especially for EVs. However, Wies explains there are also issues here related to perception and real-world use.
“We optimize [tread design] on a surface specified by ISO, and the noise we generate is normally 69dB at 80km/h. If I run the same tire on a motorway in the UK, it can naturally be louder,” he says.
For consumers, especially those unburdened by engine noise, that translates into interior noise. Reducing this is as much the responsibility of the vehicle OEMs as the tire manufacturers.
“The EU label only measures the exterior noise,” Wies says. “On interior noise, we have done a lot with products such as our Conti Silent technology. We install it to de-tune the resonance frequency of the pneumatic tube. If we do that in combination with the resonance frequency of a chassis, we can reduce the noises perceived, which are particularly annoying inside the passenger compartment, by up to 9dB, which is a lot.”
Vehicle homologation also plays a significant role in noise reduction, particularly when testing exterior noise under acceleration when the effects of the tire block structure can be louder.
Drowned in sound
Tire noise is even more pronounced on truck applications. Here, Wies says, they are researching not just the noise but the tonality as well.
“Truck tires are significantly louder, as their tire cavity is much bigger,” he explains. “If you take the German autobahn for example, [from] 1km away you can hear this noise of unfavorable tonality from truck tires because they are not pitched. They don’t pitch because of mileage and irregular wear phenomena.”
Predicting levels of tire wear is extremely important for truck operators, as well as for the wider automotive industry in general, and this is where sensors come into play. Wies believes these technologies could have been incorporated decades ago.
“I worked on sensors when I was young,” he recalls. “It was possible, 30 years ago, to put an RFID tag somewhere in the tire but no one took it, saying there was no business case and no willingness to pay. Now companies such as Tesla ask us for a sensor that can send information directly via Bluetooth – and now we have the sensor on the truck tires.”
Sensors play an even bigger role in the fleet industry, where they can monitor not only inflation pressure and temperature but also vehicle load and tire wear. They have a crucial role to play when it comes to predictive maintenance, generating vital data that can ensure fleet managers know well in advance when a tire will need replacing. Sensors are useful in motorsport applications and for performance cars, and play a key role in autonomous functionality. Ultimately, Wies expects them to be integrated into conductive rubber.
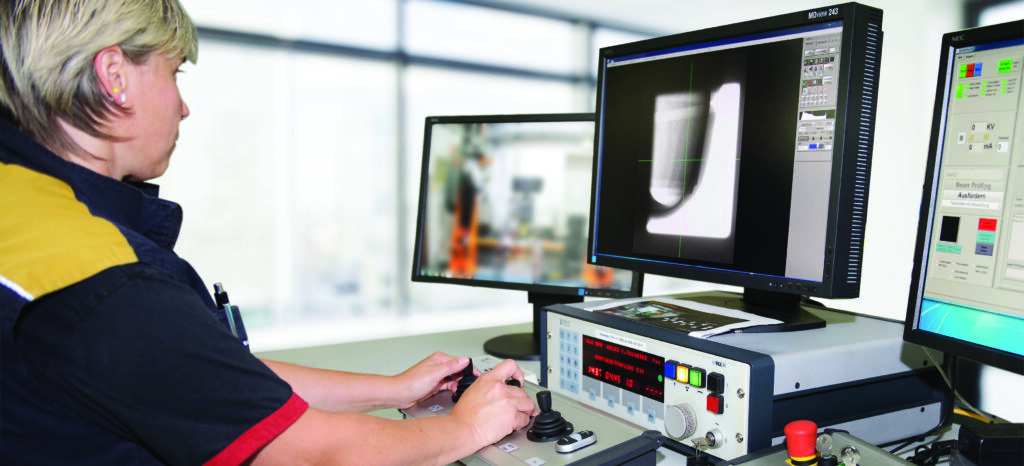
Some of these technological advances may be years, or even decades away, but R&D progress is manifesting more rapidly than ever, thanks to simulation and artificial intelligence. As is common across the automotive industry, Wies and his team are already seeing significant reductions in development and testing times.
“For a target approval loop, we used to take months, but now this can be reduced significantly,” he says. “Even tire development loops can be reduced by 50-80%.”
Continental is also investing significantly in technologies and processes along the entire value chain. A new driving simulator at the company’s Contidrom facility, for example, supports this.
“If our test drivers sit in the simulator cockpit in the future and less at the wheel of a vehicle, around 100,000km less will be completed each year on real roads or test tracks,” Wies explains.
Simulation also enables closer cooperation with vehicle OEMs. Now, small changes can be agreed rapidly during a virtual test, with multiple experts around the world working at the same time.
Technological developments are moving at speed, but what really excites Wies is the focus on circularity, as part of Continental’s sustainability goals. He has a lot of very interesting ideas, some of which are already in the research stage.
The Conti GreenConcept tire, for example, leverages both current and emerging technological approaches to the engineering of sustainable tires for passenger car applications. The tire boasts a particularly high percentage of traceable, renewable and recycled materials and, Conti claims, has an innovative, lightweight design that conserves valuable resources. The tire also features an extended service life thanks to a renewable tread.
Retreading represents a preferable alternative to decomposing old tires. Here, Wies also has another interesting idea that he calls “the zipper”. Essentially this enables the tread to be removed from a tire, either leaving behind fresh tread or allowing a new tread to be attached – or zipped on, in other words. In many ways, it sounds similar to current retreading practices but without the need to return the tire to a retreading plant to go through the buffing process.
Like many of Wies’s ideas, the zipper is currently in the research labs – as is his vision to completely replace the tire’s polyester carcass with other materials. What he does not appear to be researching is the idea to take the air out of tires completely. There have been many concepts for airless tires in recent years, particularly at technology shows, but Wies remains unconvinced by any of them. He believes there will continue to be a need for pneumatic tires, especially for autonomous vehicle applications, which consistently need four perfect tires to operate correctly.
Unsurprisingly, Wies is keen to hold back a few of his ideas – after all, he has to keep some secrets. But while he embraces technology and change, he also sees many of the traditional elements of the tire, and the tire industry, continuing for many years to come.