The tire industry is facing unprecedented challenges. As demand for tires grows, sources of natural rubber and carbon black are under pressure. Sustainability pushes are driving new green manufacturing and renewed emphasis on recycling/tire afterlife. Growing ridesharing and expanded delivery/logistics fleets are driving needs for lighter, more resilient tires. As tire manufacturers consider how to meet these challenges, leveraging new digital technologies is not only beneficial, but essential.
Leaders in tire pre-production are achieving breakthrough innovation using digital twins – a dynamic digital replica of a tire and vehicle system across its lifecycle that uses comprehensive data, analytics, simulations and emulations. Digital twins incorporate five types of interrelated models:
- CAD – Geometric and polygonal models provide digital representations of a tire’s physical composition and geometry.
- Physics – Digital models of a tire’s physical dynamics such as heat exchange, pressure, vibrations and sound.
- Automation – Models of production and automation processes, which are used to digitally emulate tire production processes so they can be studied and improved.
- Extended reality – Digital representation of the human experience with tires and tire production including observation, maintenance, operations and training procedures.
- Analytics – Digital characterization of the data, measurements, sensor readings and telematics of the tire, vehicle system and manufacturing assets used to produce the tire.
Digital twins deliver uncommon innovation, faster time to results and lower risk by using virtual models in place of costly and difficult physical experimentation and analysis processes essential in product discovery. Market leaders are seeing double-digit results across all areas of pre-production from concept to launch. The five pre-production phases are outlined below with benefits achieved from tire producers at each stage.
Concept: In this phase, companies seek to evaluate the market opportunity for new tire concepts and assess fit with current strategy. One tire producer uses artificial intelligence (AI) to bring together real-world data on raw materials with advanced analytical data that enables scientists to more accurately predict the properties of compounded rubber before use. The digital twin accelerates the development of high-performance tires that could not be achieved with traditional physical experimentation.
Feasibility and planning: Here, companies develop the technical approach for a new tire product and determine its feasibility. One producer uses digital-twin emulation on numerous unique material compounds to select the ideal ones. This market leader was able to produce a special tire for hybrid vehicles that featured a 30% drop in rolling resistance without any compromise to safety-relevant properties.
Development: In this phase, companies develop the tire and verify its functionality and performance while designing production processes and introduction plans. It is a costly and difficult set of processes. A tire producer set out to dramatically improve radial passenger tire building with advanced machinery to increase labor productivity, output, quality and ease of setup. A team used analytical models and machine learning to characterize data, measurements, sensor readings and telematics of production manufacturing assets. They were able to optimize tire-building performance, delivering more than half a million tires per year in production potential per plant.
Test: At this stage, pre-production teams stabilize operational, service and support processes, and transition responsibilities to operations. One company changed its approach from designing, building and testing physical prototypes to a more streamlined approach using advanced simulation. Using a digital twin, its engineers could leverage complex simulations to reduce expenditures on pre-production building and testing by 25%.
Launch/In-market: In the final stage of pre-production, the tire product is launched and teams assess tire product performance to find opportunities for future improvements. One global tire leader uses AI to monitor and learn from driver behavior, tire pressure and performance. The company developed a connected tire sensor solution for a commercial fleet, which has helped them achieved double-digit improvement on tire-related functional problems, including breakdowns and safety.
Rockwell Automation works with tire producers across each stage of the pre-production process. Through our experience, we’ve identified five key steps to implementing a successful digital twin:
- Map out your digital twin strategy. Understand the pre-production dynamics that impact value creation and surface the opportunities that must be addressed.
- Create digital twin project pilots to prove value. Empower a dedicated team with the resources needed to drive a successful, transformational pre-production process.
- Define the capabilities you need. Building on the lessons learned in pilots, define the capabilities needed to achieve your vision.
- Become digital twin wizards. Identify the digital twin insights that will unlock competitive-advantage and marketplace success.
- Transform pre-production. Maintain a sense of urgency. Communicate and demonstrate that you cannot ‘return to the old way’.
Through digital twins, the tire industry can unlock double-digit impact across the phases of pre-production. The data and technology leaders that embrace this new approach will better position their companies to be innovative, resilient and competitive for the challenges that lie ahead.
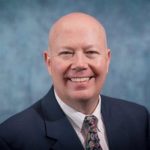
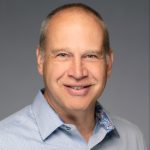