According to Identec, there are four big issues costing tire plants millions every year
In tire manufacturing, the shopfloor logistics necessary to get the right material, the right tire building machine, at the right time, are complex. This process is costing most tire manufacturing plants millions of euros annually.
According to Identec, the four biggest issues are:
• expired raw material;
• time lost searching for the right material carriers;
• productivity loss by inserting the wrong material carriers into the machines; and
• lost productivity due to scanning and electronic booking issues.
Expired raw material
Mixed raw material has a limited shelf-life and almost all tire manufacturers are wasting some percentage of expensive material due to the expiration date being exceeded. The challenge is getting the required material to the right tire building machine before it expires. That may sound rather easy. However, considering that even a relatively small tire manufacturing plant can have thousands of material carriers in use, it becomes clear why just about every plant is battling the issue of expired raw material. An average size plant easily loses €150,000 annually due to this issue.
Searching for material carriers
Raw materials are transported to tire building machines on material carriers. These are loaded in preparation zones, then get moved to interim storage areas before being delivered to the tire building machines. Following the production run, these carriers are either sent back to the preparation area for reloading or temporarily stored for reuse in a second production cycle.
Since almost every plant uses numerous compounds and varying material carrier types, servicing many tire building machines, the chain of events is quite complex. Finding the right carrier at the right time is a big challenge for almost every tire builder. The time spent searching by material carriers adds up fast and is costing tire builders dearly.
Productivity loss by feeding the wrong material carrier into the machine
Tire building machines have many raw material bays. The machine operator relies on logistics personnel who, with the help of the production management system, deliver the material carrier to the correct machine or material bay. Unfortunately, time and time again, the wrong carriers are fed into the machine bays. This can be due to the logistics staff delivering the wrong carrier to the staging area or the machine operator grabbing the wrong carrier.
To address this, most tire manufacturers have a validation system installed to guarantee that no tires are produced using the wrong material. The problem is that if the wrong carrier is inserted the error is only discovered once the new material has been spliced by the machine operator, who then has to walk around the machine to check the control panel where any faults are displayed. The operator now needs to walk back to un-splice the material, remove the carrier, find the correct one, and finally insert and splice the correct material. The operator must then return to the control panel to run the machine.
During this whole time the tire building machine is standing idle. This lost productivity can easily add up to several hundred tires per day per plant. This issue alone can quickly result in lost profit of over a million euros annually.
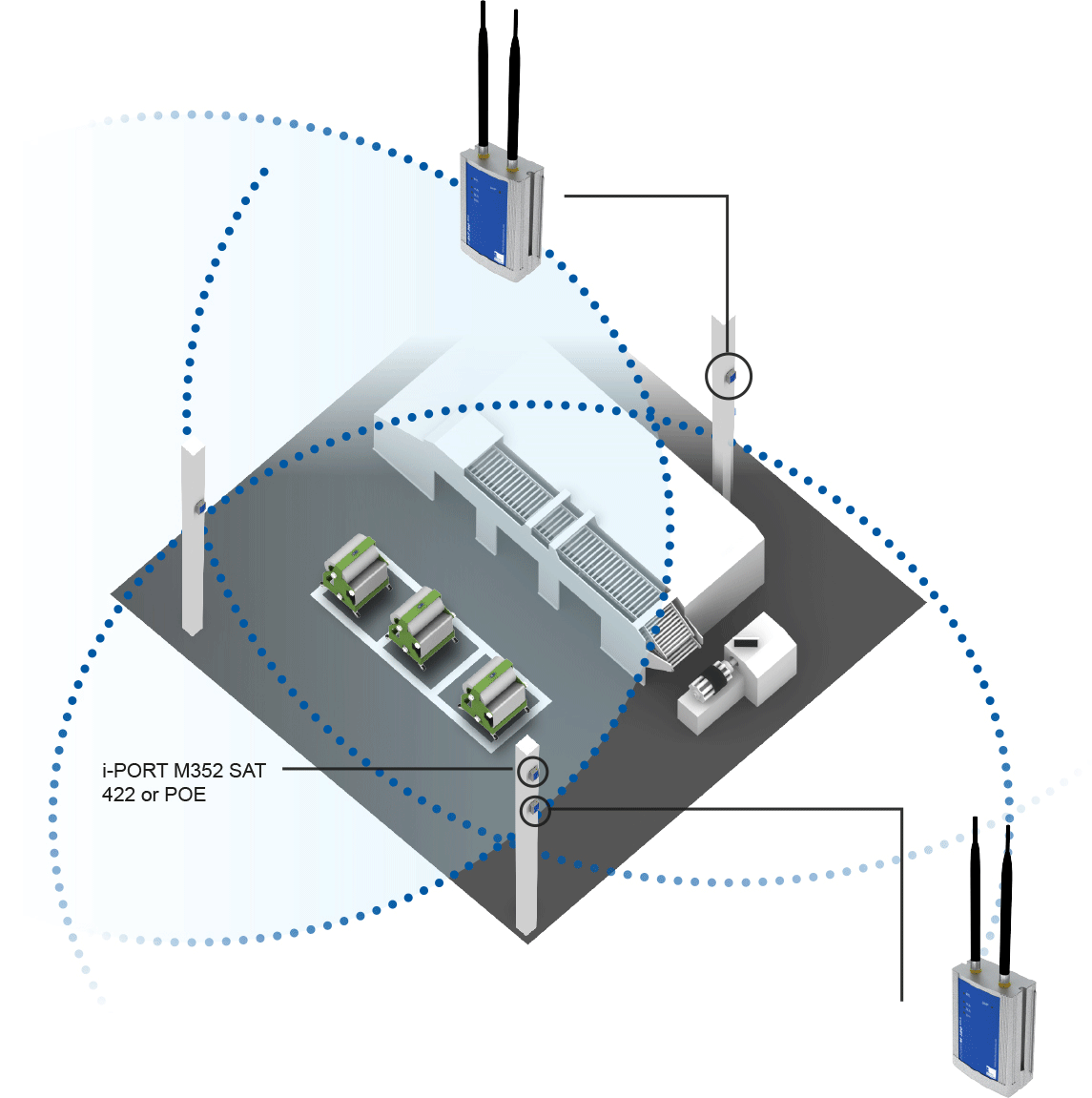
Lost productivity due to scanning and electronic booking issues
Most tire manufacturing plants use a scanning system to identify material carriers and the associated raw material. This of course means that the production management system is reliant on the manual scans performed by operators or logistics staff.
In addition to the time spent scanning, it is well known that manual processes are a common source of error. The biggest problem with this procedure is that the operator doesn’t get instant feedback should a carrier be matched to the wrong machine. The problem only becomes apparent once the operator tries to run the machine.
In addition, some manufacturers use automatic scanning within the machine bays for validation purposes. This can also present problems if the barcode label cannot be properly read. All of this inevitably leads to the standstill of the tire building machines while the issues are fixed. This can easily add another million to the profit loss.
The solution
There are solutions available to address these challenges. The answer is to know the exact location of each material carrier accompanied by an intelligent verification system and the complete removal of barcode scanning processes. There are systems available, which enable even smaller plants to significantly improve productivity, by solving the problem of expired material and reducing the time needed to find material carriers.
How is it done?
The material carriers are fitted with transponders, which communicate their location in real time. These positions are used to instantly generate automated bookings in the production management system, thus eliminating the need for manual scanning.
Logistics staff responsible for the distribution of material carriers are equipped with industrial handheld PCs displaying transportation orders complete with pick-up and drop-off points. To assist in finding the carriers, some manufacturers equip the transponder with multi-color LEDs. Personnel looking for a specific carrier can initiate a blinking of the transponder, which enables immediate visual recognition of the carrier (pick-by-light). This is especially useful in areas where large numbers of carriers are stored in close proximity to one another. This dramatically reduces search times. There are transponder types available that can also be configured to give the machine operator instant visual feedback, should the wrong carrier be inserted into the tire building machine.
With the right material in place, there is no need to re-splice and return to the control panel. Any error is immediately recognized. Another useful feature could be a visual signal from the transponder should the right material be used, but in the wrong order. This enables instant feedback to ensure that the oldest material is always used first.
These are just a few important technical features of a management solution in tire production, all of which contribute to less waste, and increased data quality and productivity – resulting in additional profits of millions annually per plant.
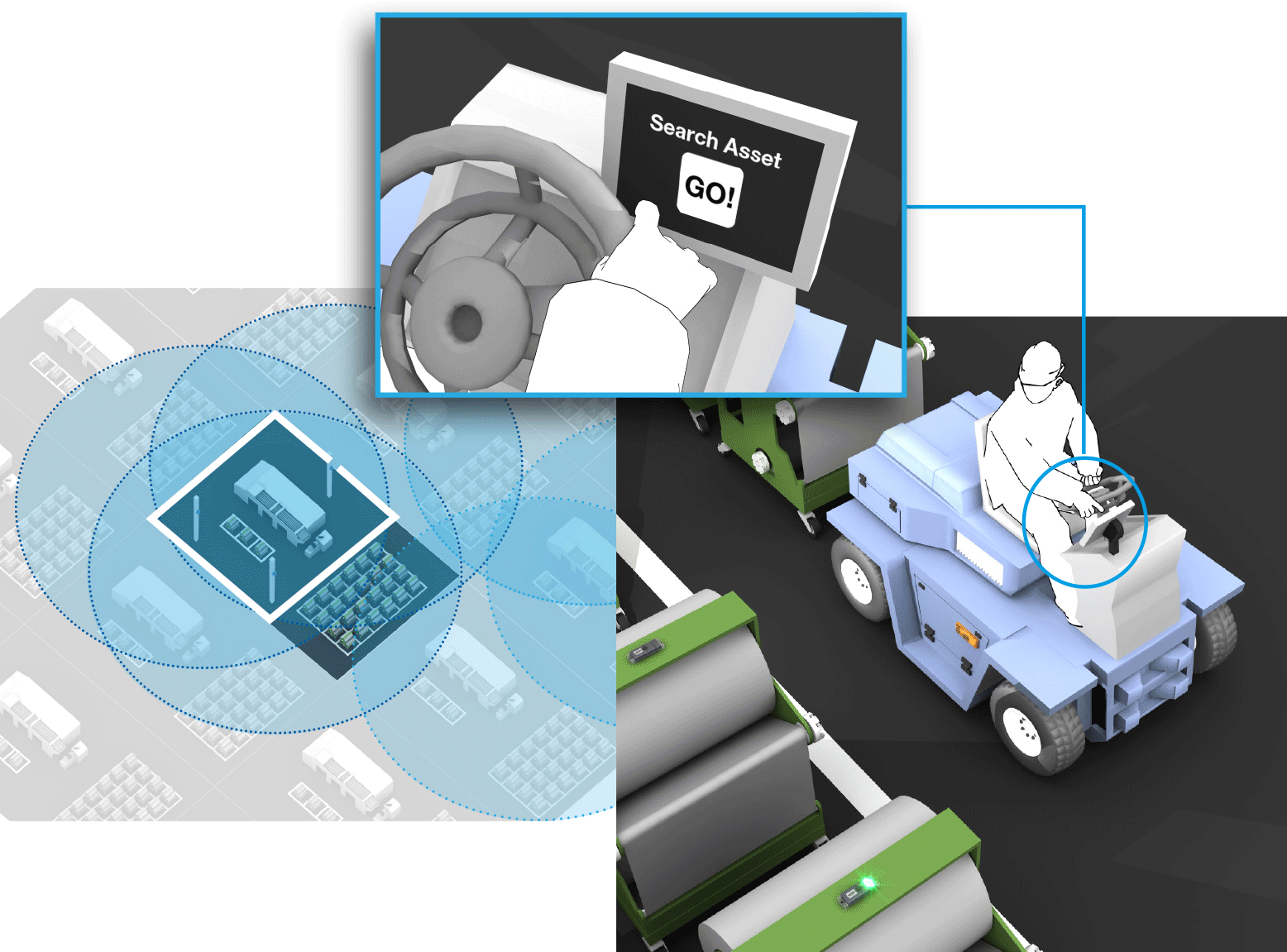