A team at Coventry University in the UK have developed a novel active safety concept that could offer a breakthrough in preventing road accidents and saving lives on wet roads. The device is primarily designed to prevent accidents caused by aquaplaning, but could also save lives by drastically reducing braking distances in the wet.
Such work could be interesting for companies working with tire sensors that can detect the onset of aquaplaning, in regard to how the information would inform the activation of the device.
Development of the device
Aquaplaning occurs when a layer of surface water builds up between the tire and the road surface leading to a complete loss of grip. Aquaplaning is extremely dangerous and can occur at a speed of 50mph (80km/h) with as little as 2-3mm of standing water.
To address the problem, a new concept referred to as the Run Dry Tyre System (RDTS) was developed by Prof. Mike Blundell and patented by Coventry University.
The main operating principal of the RDTS invention is that by firing a jet of compressed gas close to the front of the wheel and the road surface, it removes surface water in front of a vehicle tire to ensure that the tire rolls into a dry patch of road surface.
The prototype (Figure 1) was fitted to a Coventry University research vehicle and tested at Horiba MIRA on the aquaplaning and wet road surface test facilities.
The initial prototype was built using a small canister of compressed CO₂ gas that can be bought ‘off the shelf’, and used a manual switch to activate a solenoid in order to release the compressed gas from the canister. For this first development of the system, the RDTS device was fitted to the front wheels only, and a cannister was selected that would provide one second of continuous blast for the compressed CO₂ gas.
How the tire sensors detect the conditions that trigger firing of the system, and the design of the mechanism that deploys the system from a stored to an active position, could be developed in collaboration with an industrial partner.
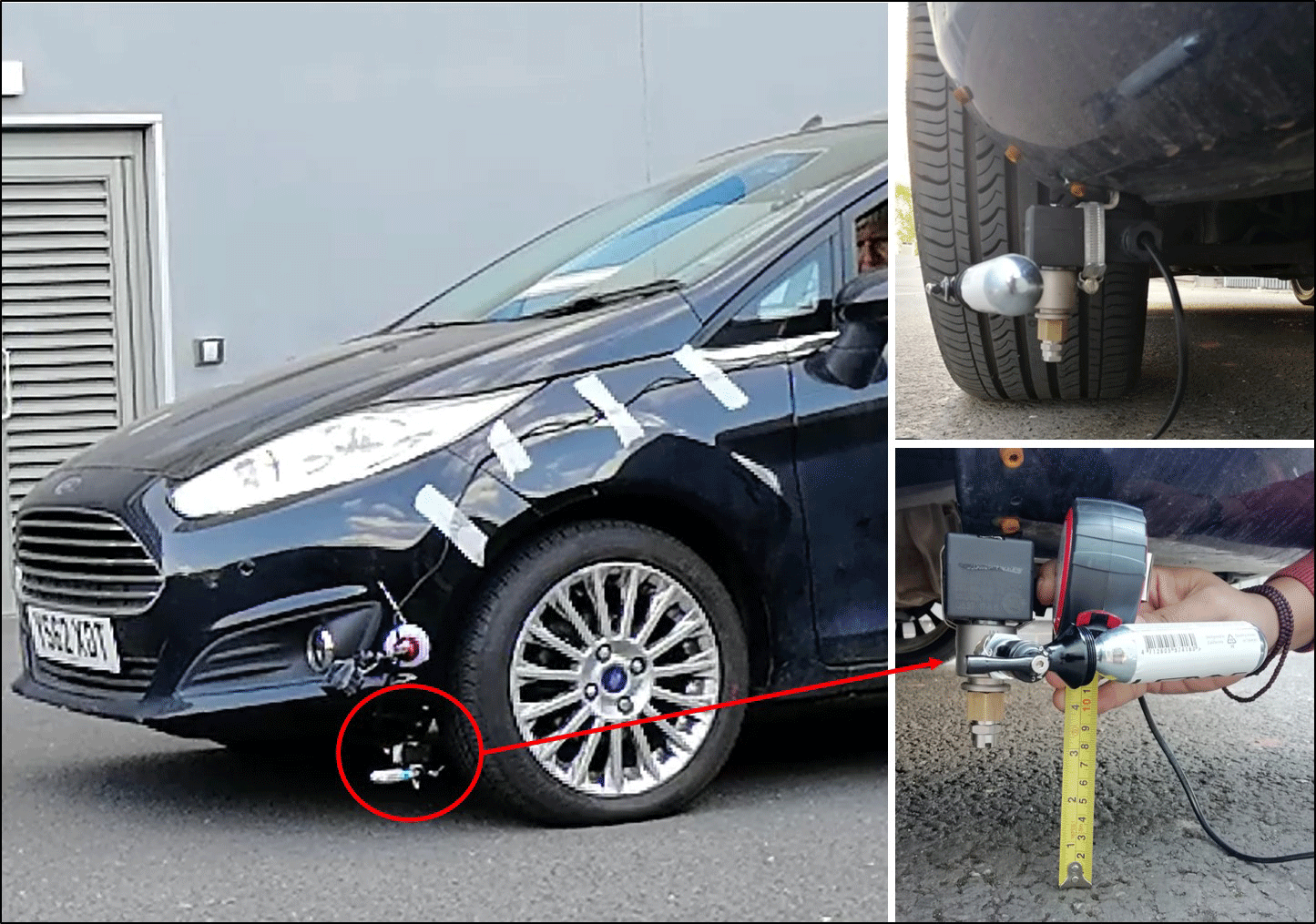
Testing the system
Before visiting the proving ground, initial tests were carried out with the vehicle being driven through an area of standing surface water at 30mph (48km/h). In Figure 2, the dark V shape in front of the tire is the dry patch of surface road that was successfully created in front of the moving tire.
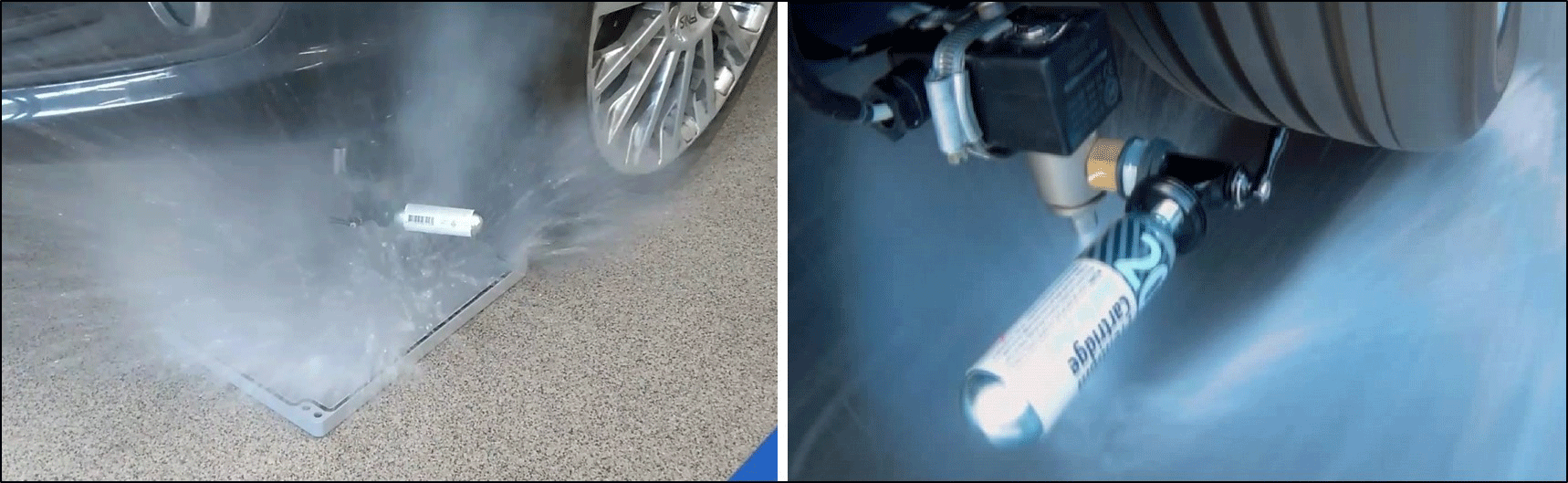
The Horiba MIRA test surfaces provided a perfect environment to test the effectiveness of the system under controlled conditions. The main surface used was a bespoke aquaplaning track, which is 66m-long and enables the depth of water to be varied. For these tests, the depth of water was kept close to 5mm (0.2in). Other surfaces such as the wet asphalt and basalt test lanes were used to investigate improvements in braking distance.
These specialized test surfaces can recreate the low friction conditions that drivers might encounter in the real world. The friction coefficient for the wet basalt is 0.30, which is very close to icy or wet snow conditions. For the wet asphalt surface, the friction coefficient is 0.75 and for the wet concrete surface the friction coefficient is 0.40. If aquaplaning occurs on the aquaplaning test track, then the friction coefficient is effectively zero.
For all of the tests, measurements were first taken without using the system, and then the tests were repeated when firing the RDTS. This allowed a direct comparison to establish any improvements achieved when the RDTS was used. The system was tested at various speeds from 30mph (48km/h) to 70mph (112km/h).
For the braking tests, some significant improvements were achieved. In some cases the reduction in measured braking distance was very clear, particularly on the wet basalt, where a 22% reduction in braking distance was obtained at 50mph (80km/h). Peak deceleration was also recorded, and for this output the best result obtained was again at 50mph on the aquaplaning track. In this test the peak decleration was increased from 0.37g to 0.59g, an almost 60% improvement in performance. During testing, the vehicle occupants could also physically feel the inertial effects of the increased braking deceleration when the RDTS was fired.
The overall ambition is to develop a proof-of-concept that can produce almost dry road conditions when the system is fired in wet conditions, while adhering to the design principles that the system should be modular, lightweight, inexpensive and easy to package.
The university invites any interested automotive OEMs or Tier 1s to collaborate in the development of what they hope will be the introduction of a disruptive technology. Companies developing tire sensors that can detect the onset of aquaplaning could be interested in how the information would inform the activation of the RDTS.